Much like the ajrakh block printing which was the subject of my last post, another resist-dyed textile craft of the same area – Kutch in north Gujarat, is bandhani or tie-dye. Like ajrakh its rich pattern and texture gives it the ability to sparkle and entrance the viewer or wearer. The tiny white dots created by meticulously tying thousands of sections of the cloth to resist the rich colours of dye it is then dipped in, create an illusion of stars in the night sky, much like the resist-printed patterns of ajrakh. Worn as odhini (shawl), choli (blouse) and gaghra (skirt) by women in many communities all over Gujarat and Rajasthan, this affect is heightened as the fabric shimmers and sparkles with every movement the wearer makes.
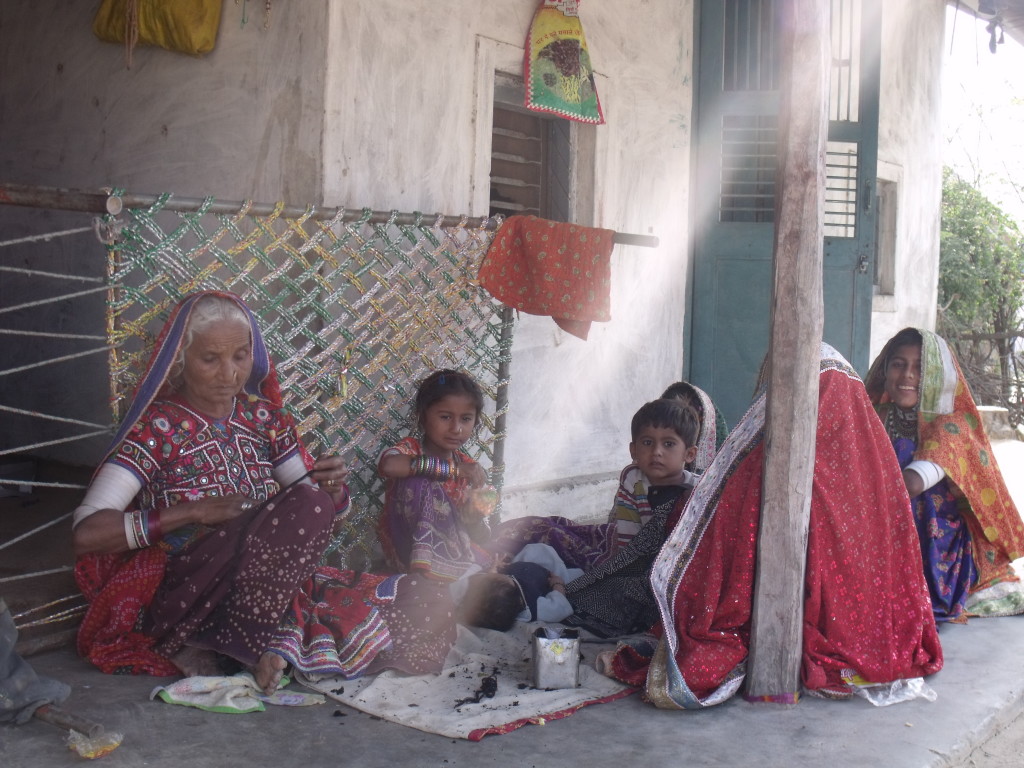
Origins
The name bandhani derives from the Sanskrit words bandhana and bandha meaning ‘to tie’. It is from this word that the English named bandanna for the spotted handkerchief came from when traded to Europe from India.
Again like ajrakh, bandhani’s presumed origin dates right back to the Indus Valley Civilisation. The mordant dyeing equipment found at the famous Indus site of Mohendjodaro suggests these dyeing and printing methods could have been in practice this far back. This is further suggested by the stone statue of a Brahmin priest wearing a patterned scarf, which some believe could have been printed. However, more accurate evidence of the practice of bandhani in ancient times is the Buddhist murals at the Ajanta Caves in Maharashtra depicting female figures wearing bodices with spotted pattern and ikat skirts. Amongst the textile fragments unearthed at the medieval site of Fostat, near Cairo, which included block-printed fabrics from Gujarat, were block-printed patterns imitating tie-dye. Imitated bandhani printed patterns are still widely block printed and screen printed today.
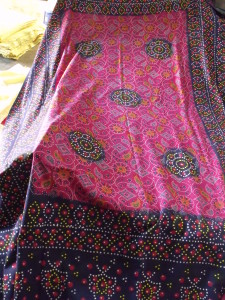
The wearing of bandhani serves as a marker of identity in many communities in the regions it is produced, and features strongly in the wedding outfit due to its perceived auspicious qualities. The finer the bandhani, the more expensive it is, and thus, very fine tie dyed odhnis are worn by women in the richer communities of merchants, landlords and the higher class of craftsmen.
The craft is practiced by Khatris in Kutch, in Bhuj, Abdasa Taluka, Anjar and Mandvi. Saurashtra in Southern Gujarat has larger bandhani workshops in Jamnagar, Porbandar, Morvi, Rajkot and Wadwhan near Surendranagar. Bikaner, Jodhpur, Barmer, Jaipur and Udaipur are a few bandhani centres in Rajasthan.
Process
The traditional process involved placing fabric over nails set in wood blocks and tying the fabric by pinching it over the nails with the thumb and forefinger. However, more modern methods involve transferring the pattern onto the fabric using these same blocks with inserted nails, or carved wooden blocks and printing with a paste of geru – a red ochre. However, a more common method is stencilling the patterns using a pierced plastic sheet and a fugitive dye mixed with kerosene.
The tying is usually done by women, and the dyeing by men. The fabric is pinched at each marked dot and pushed into peaks helped by a finger nail or small metal point, and thread is tied around about 6 to 8 times. A knot is looped around and the same line of thread is used to tie the next dot, and so on.

The fabric is often folded to make the processes quicker, while also creating a mirrored design. The number of stages of tying and dyeing depends on the number of colours and complexity of the design. The dyes used are usually synthetic, but like other dyeing and printing crafts in India, natural dyes are being revived, and are particularly popular amongst foreign and urban markets. After being dipped into the dye, the fabric is dried, then stretched out to reveal the pattern. Often the bandhani cloths are sold with the threads still on the cloths to prove it is a genuine hand tie-dyed article, and the customer then has the pleasure of revealing the pattern for themselves.

Contemporary bandhani
In the last few decades, bandhani has experienced success in Indian urban and global markets. Adapted designs, new colours, natural dyes and new garments made by skilled craftspeople using the traditional technique can be found in up-market shops all over India and abroad. These include Bhandej (a variation of the word bandhani which also refers to the tie dye technique), Aranya Naturals in Kerala whose focus is natural dyes and also produce block print and hand painted cloths, Anokhi who have shops in cities all over India, Kala Raksha and Khamir in Kutch.
Kamaldeep Kaur – Neelgar
An individual who has worked hard to keep the traditional craft of bandhani skills going, and put the craft on an international platform, is consultant designer and researcer in natural dyes, resist dyeing and printing, Kamaldeep Kaur, also known by her company name Neelgar.
After completing a two year fashion design diploma in Delhi, Kamaldeep worked for various top fashion houses and boutiques followed by a spell at the Gujarat State Emporium in Ahmedabad. Here she worked extensively in the villages with various traditional artisans. The resulting products in GURJARI– the shops for the Gujarat State Handicrafts Development Cooperation, were admired by many companies and encouraged her to develop her own production of soft furnishings and garments. After many successful projects with artisans in Gujarat offering her design expertise to help build their markets, Kamaldeep specialised in bandhani.
She started with a task force of eight women and is now supporting about 200 families, training them in design and quality. A piece can take from four weeks to one year to produce depending upon the design .So far the largest number of dots/ knots in a piece has been approximately 80 thousand and it took a year to make.

Kamaldeep tells me that recent collections have been inspired by different cultures, traditions and nature. She has been particularly inspired by Japan, Africa and Malaysia. For example in a recent piece she has taken motifs used in Malaysian ikat and translated them in a bandhani pattern. Kamaldeep explains that her recent focus has been on quality and to promote this quality all over the world, informing people of the rich traditions in craft and the high level of skill of craftspeople in India, and with an aim to rid the view of India’s cloth production existing solely of the cheap mass-produced garments.
Khatri Alimohamed Isha
Alimohamed is one of a few hereditary artisans of bandhani who have become well known in contemporary markets for producing very high quality, fine bandhani scarves and garments in silk, wool and cotton. He lives and works at Khatri Chowk in Bhuj, named after the high concentration of Khatris of printing and dyeing who have lived there for centuries. He travels all over the world to give workshops, promote the craft and sell his work. He also receives visitors from all over the world including textile tour groups, buyers, collectors and museum curators. I took part in a workshop with Alimohamed and his son way back in 2008 and having a go at this craft made me realise how skilful it is. My attempt was a very inferior piece with huge resist dyed sections, not able to master the tiny dots that the skilled women produce. Alimohamed is on the board of master craftsmen advisors at Kala Raksha Vidhyalaya, helping young aspiring artisan-designers keep in touch with their traditional craft while creatively innovating upon these and making them relevant to contemporary markets.
Abduljabbar Khatri
Also based in Bhuj, Abduljabbar and his brother Abdullah whose business is called SIDR Craft, are known for their innovative contemporary productions of bandhani which have featured on the catwalks of Mumbai fashion week, and like Alimohamed, at international fairs and exhibitions such as the renowned Sante Fe International Folk market. Also like Alimohamed, Abduljabbar and Abdullah have revived the use of natural dyes in bandhani production and has achieved a beautiful array of rich colours derived from madder, indigo, turmeric, rhubarb, logwood and weld.

Abduljabbar said he and his brother grew up at an interesting time – when there was an increasing interest in traditional craft amongst government and non-government initiatives and foreign markets, along with an inspirational family – their father had received a Bachelor of Arts, and their uncles and cousins who became expert dyers, reviving the craft following its decline in their family during industrialisation. These influences led to Abduljabbar to apprentice in tie and dye workshops and study a Commerce course which led to working full time on their craft. Both brothers have since received the UNESCO seal of Excellence and other awards, and demonstrated and exhibited at workshops, fairs and exhibitions all over the world.

To fully experience and appreciate bandhani though, it must be touched, felt and worn to really get a sense of the softness of the silk and the rich texture of the tied pattern. Here are some suppliers of brilliant bandhani:
India: Anokhi, Kala Raksha, Bandhej, Khamir
Canada: Maiwa
UK: Joss Graham
Travel Information
Or you can visit Ahmedebad, Bhuj and the surrounding villages to see the craft in action.
I visited the bandhani artisans while on a tour with Desert Traditions. The tours are run by Australian Carole Douglas, who has long-standing relationships with many of the artisan communities the tour visits, all of whom have a great deal of trust in Carole. She has also led projects, curated exhibitions and facilitated market outlets for many of the artisans. This makes the visits to artisans friendly and comfortable. There is also a strong focus on being responsible and sensitive to the environment and communities visited.
I also recommend local tour guide Kuldip Ghadvi who runs Kutch Adventures India. Kuldip runs more general tours around Kutch specifically, is from the area so has deep knowledge and experience, as well as good relationships and reputation with the people he visits.
2 Comments
Margot Renton
very interested in your blog – keep the stories coming!
Thank you
faiz khatri
Dear sir,
I mr faiz khatri Manufactour of Kutchhi Hand Tie & Dyed bandhani process since 1960
Products – Duppta , Salwar kameez , Chaniya Choli , Scaf , Stole , Saree…..Skart , Top…etc
Materiyal – Cotton , Cotton shatin , Silk , Gaji silk , Georgate , Seaphone , Creap , Samo Shatin , …..etc
Degain – Mable Dyed , Sibori ( its made by needle ) , Laheriya , Malti Gulti , Descharge ,
Fenshi Degain , Tie & Dyed , ….etc…..
If you want to see some images of kutchhi Hand Tie & Dyed bandhani scarve sarees , dress material , dupptas , chaniya cholis……with our fecotary work such as how do tie & dyed…
please visit – http://www.faizhandicrafts.blogspot.com
.
Plz contact me for more information
In Case if have any question fell free to write me
Thanks
-faiz
FAIZ HANDICRAFTS
Danda bazar
Bhuj kutchh, Gujarat
370001 india
mob- +91 -99795 25795
contact person -faiz khatri
EXPORTERS AND MANUFACTOUR OF
WOMEN TEXTILE GARMENT
SPECIALIST – KUTCHHI HAND TIE AND DYED
“BANDHANI” PROCESS
(THE FAMOUS INDAIN HANDICRAFTS
E-MAIL – faiz_handicrafts@yahoo.co.in