I have just returned from a month long trip to India, three and a half years after my last trip. After a few days of settling into a very different time zone, climate and pace of life, I soon felt quite at home, the places and people I visited seeming as familiar as if I’d seen them only a few weeks before.
A busy schedule and little access to the internet meant I couldn’t blog about the trip as I went, so this is the start of a series of blog posts in which I will write about my encounters with various textile artisans – this time mainly weavers, as the purpose of my trip was to begin fieldwork for a PhD on the traditional handloom weaving in India.
After a couple of days in rainy Ahmedabad adjusting to the stifling and sticky heat, time difference, noise and traffic, I took a night train to Kutch. I arrived early in the morning and took a rickshaw straight to the Gangaram Hotel, greeted by Mr Jethi who welcomed me home – I always stay at the Gangaram when visiting Bhuj. I was there for two weeks while I visited the surrounding villages. I spent most of my time in Bhujodi, a village about 8 km from Bhuj. At one time this would have seemed much further from the city but now as the city of Bhuj has developed and expanded, its suburbs almost reach Bhujodi.
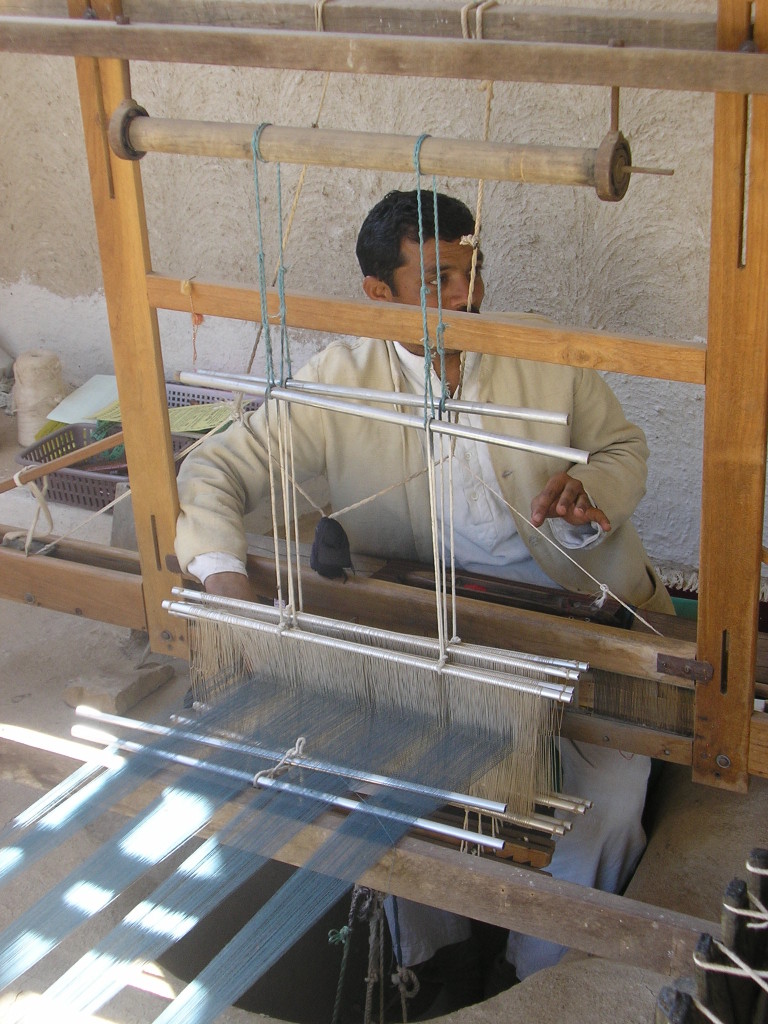
Weaving in Bhujodi
At either side of the central dusty road running through the village are non-descript concrete walls, many painted in the concrete manufacturer’s yellow lion logo, a common site all over Kutch. If it were not for the rhythmic ‘clack, clack, clack’ sound of wood on wood, having the curiosity to peer into an open door and seeing a weaver at his loom, yarn hanging to dry or a woman tying a bobbin using a bicycle wheel, you may not realise that the majority of the 1200 people behind these walls are Vankars – traditional weavers.
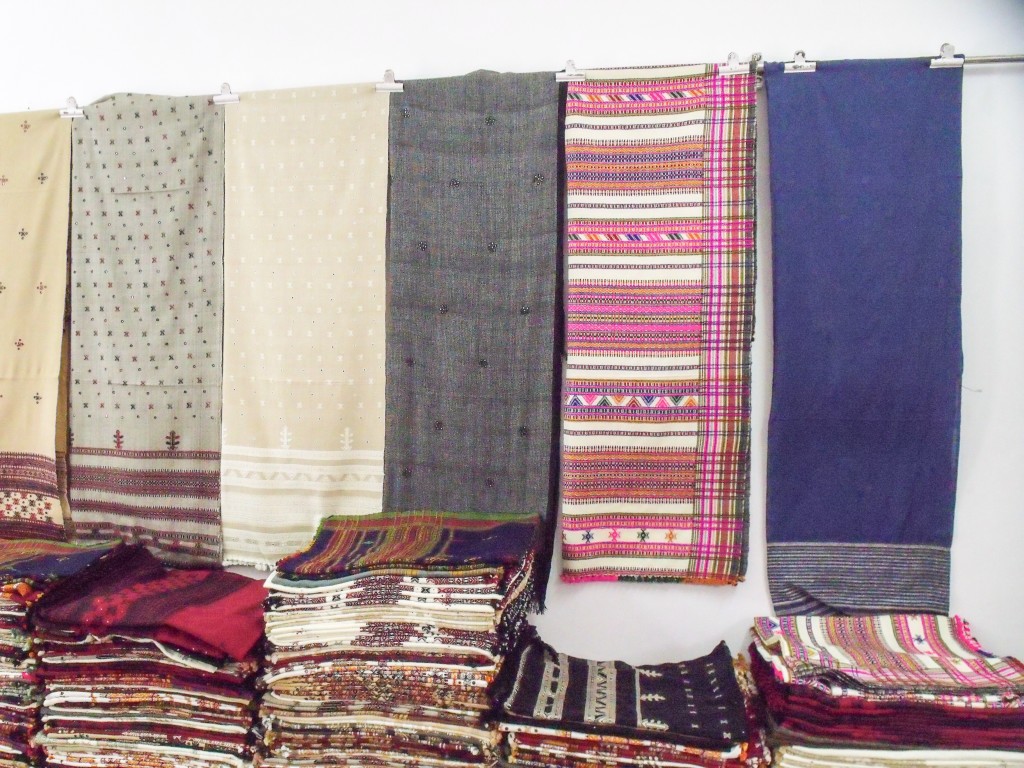
I visited Shamji, son of the renowned Master Artisan and National Award winner Vishram Valji Vankar, who along with his four brothers runs a thriving business with customers all over the world. Shamji and I had met a couple of times before – the first back in 2008 on my very first trip to Kutch, and the second when he was exhibiting in Manchester. Shamji kindly found time amongst his busy schedule to talk to me about the history of weaving in his village, which he has gathered documentation on for the last 20 years.
As well as weavers, the village of Bhujodi is also home to Rabaris, nomadic and shepherd communities who were the original customers of the Vankars along with Bharwards and Ahirs living in neighbouring villages. These communities supplied the weavers with fleeces from their sheep. In turn, the Vankars made veil cloths, skirts and blankets.
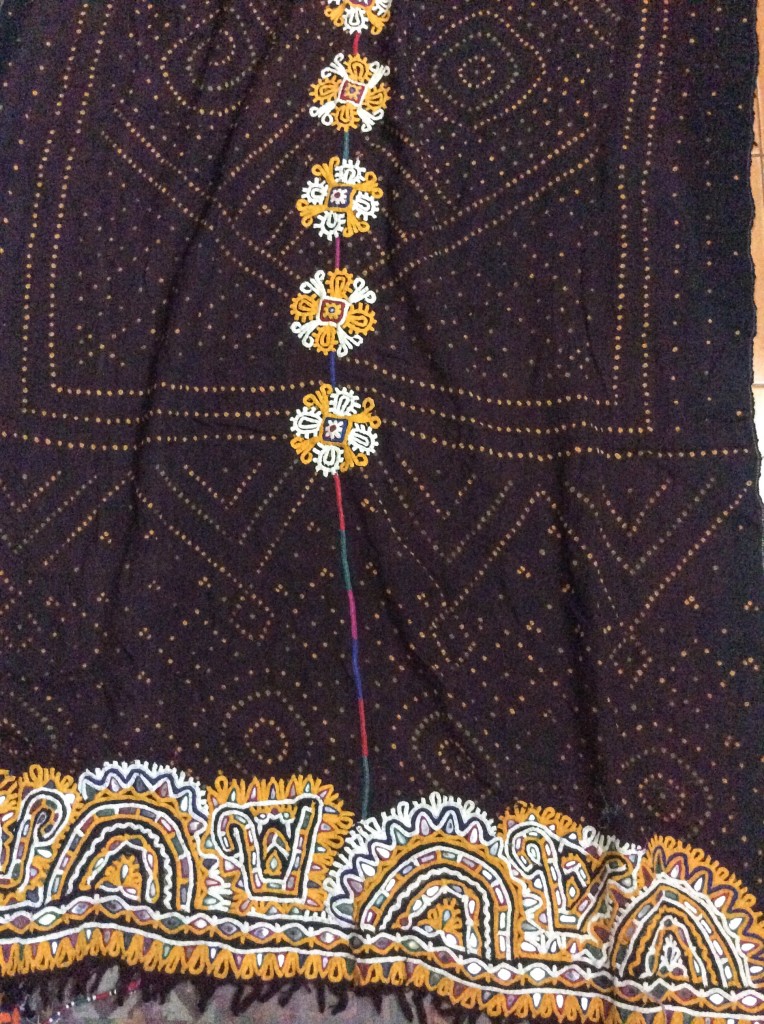
How to make a Rabari shawl
Below is the traditional process involved in the making of a Rabari shawl:
- Wool is spun by either the weaver’s family – most often the women, or the Rabari communities for who the shawl is ultimately made.
- The weaver weaves the cloth. The traditional pit looms were usually only wide enough for one half of the shawl so two pieces were woven then sewn together using the distinctive and decorative ‘fish stitch’.
- The woven cloth was then sent to the Khatris – the dyers to dye the cloth. If it was to be tie dyed, the cloth was first given to the rabari woman – the customer – to choose her preferred design. She would then give this back to the weaver who would give to the Khatri to carry out the dyeing.
- Once dyeing was complete it was given back to the Rabari woman who would embellish the shawl with dense and elaborate bright coloured embroidery.
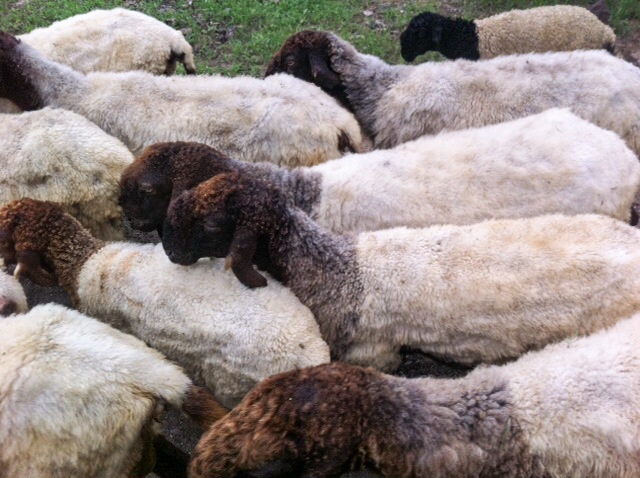
Until recently, shearing was done by the shepherds themselves. Now sheep shearers come from near the Rajasthan border twice a year to travel from village to village to shear the sheep, Shamji tells me. The local desi wool is very coarse and while it was popular for the Rabari and Ahir men as blankets (dhablo) while out in the cold harsh desert, and for the Rabari women because of their belief in its ritual purity, it doesn’t have this significance for the urban and foreign clientele who now make up the majority of the weavers’ market.
Most Vankars now use imported wool such as Merino from New Zealand, as well as cotton and silk for scarves, stoles and shawls. Shamji does include local wool shawls in his shop, some un-dyed (the natural colour of the sheep), some dyed in natural indigo, others in chemical colours, which he says are popular with foreign markets as throws.
Unless the shawl has to be piece-dyed or tie-dyed, as mentioned above, the weavers usually dye the yarns themselves before weaving, or procure ready-dyed yarns. Shamji often does the dyeing himself so he can get the exact colour he needs. Lac dye was traditionally used for women’s shawls, a dye which Shamji and others have revived over the past few decades after its decline in the middle of last century.
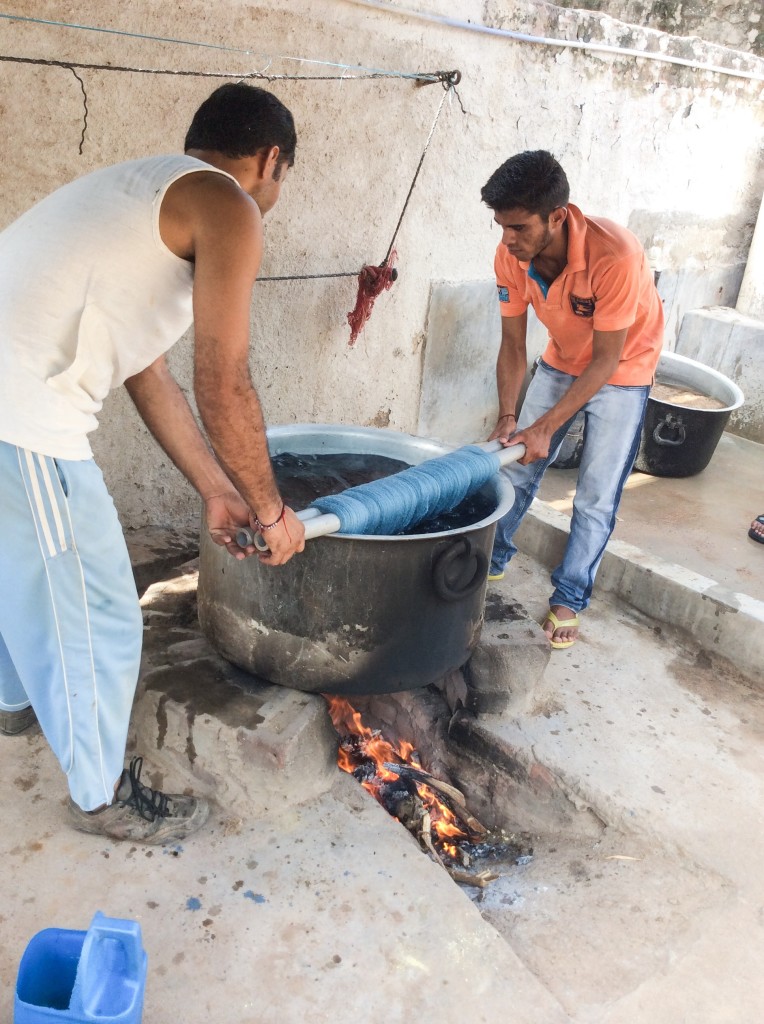
The making of a Rabari shawl using the full process as described above is not in practice as much now due to the length of time it takes, and the high cost. They are popular amongst textile collectors but the originals are getting harder and harder to come by. Modernised versions of the shawls are commissioned by some NGOs and Shamji works closely with a group of Rabari ladies in Lodai, north Kutch to add traditional Rabari embroidery in a contemporary palette to his hand-woven silk, cotton and wool shawls.
I also went to visit Dahyalal, a weaver who used to work for Shamji but after graduating from Kala Raksha Vidhyalaya, has now set up on his own. The school that began in 2005 to provide design education to artisans – encompassing drawing, colour, marketing, business and presentation – has turned many artisans of the local area into successful business men and women. Dahyalalbhai now produces some innovative contemporary pieces largely for a foreign and urban clientele. He recently sold the majority of his stock at the world renowned Sante Fe International Folk Art fair.
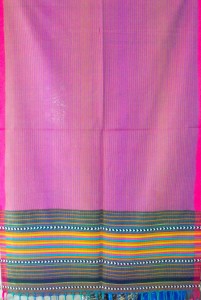
Mentoring the artisans of Bagalkot
Jyantilal is another Bhujodi weaver who used to work for a Master Weaver before graduating from KRV and now running a successful enterprise. He is also currently studying on the new initiative Somaiya Kalavidya founded by KRV director Judy Frater. As part of this course, which has a strong focus on business management and marketing, Jyantitlal and Chamanlal, another successful weaver from Bhujodi, have been mentoring a group of Ilkal Sari weavers from Bagalkot in Karnataka for a project called ‘Bhujodi to Bagalkot‘.
The area of Bagalkot is in need of development and so Judy Frater saw the potential for innovating upon the saris of Bagalkot for new markets. In a pioneering collaborative project in which artisans are working with artisans – rather than designers or buyers with artisans – each group of weavers have taken aspects of both weaving traditions and innovated upon these to make a collection of contemporary saris, shawls and scarves for an exhibition that will be held at the Artisans Centre in Mumbai from the 8th October.
But weaving doesn’t only happen in Bhujodi. There are weavers scattered in villages all over Kutch. Another such weaver is Magan Govin Vankar, another KRV graduate from Nirona village. While Magan Govin sold the whole of his KRV collection bar one scarf, he now mainly produces for the local market. He told me he’d like to produce for a wider market, but I wondered whether being separate from the well visited and tourist friendly Bhujodi made it more difficult for him.
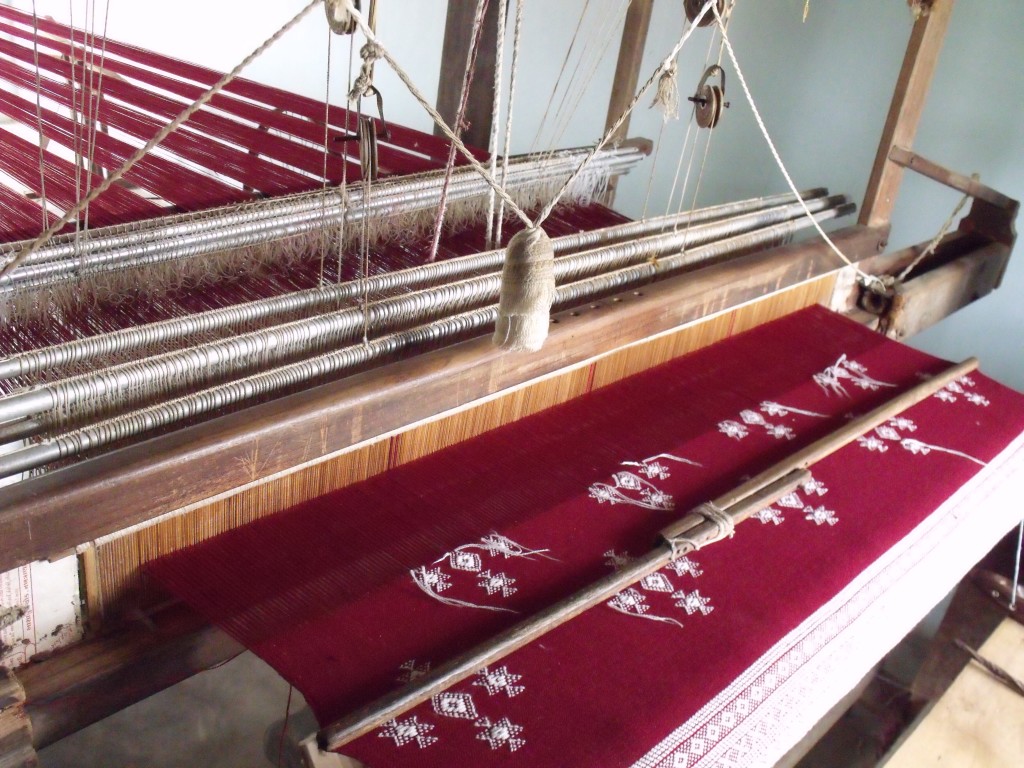
Ramji Maheshwari living in the village of Sumarasar, about 20 km north of Bhuj, another graduate from KRV and current student at SKV eagerly showed me his large collection of innovative hand-woven shawls and stoles incorporating traditional Kutchi motifs alongside ikat, stripes and checks. Ramji has done well with marketing, particularly to the tourist market for which his products are very successful.
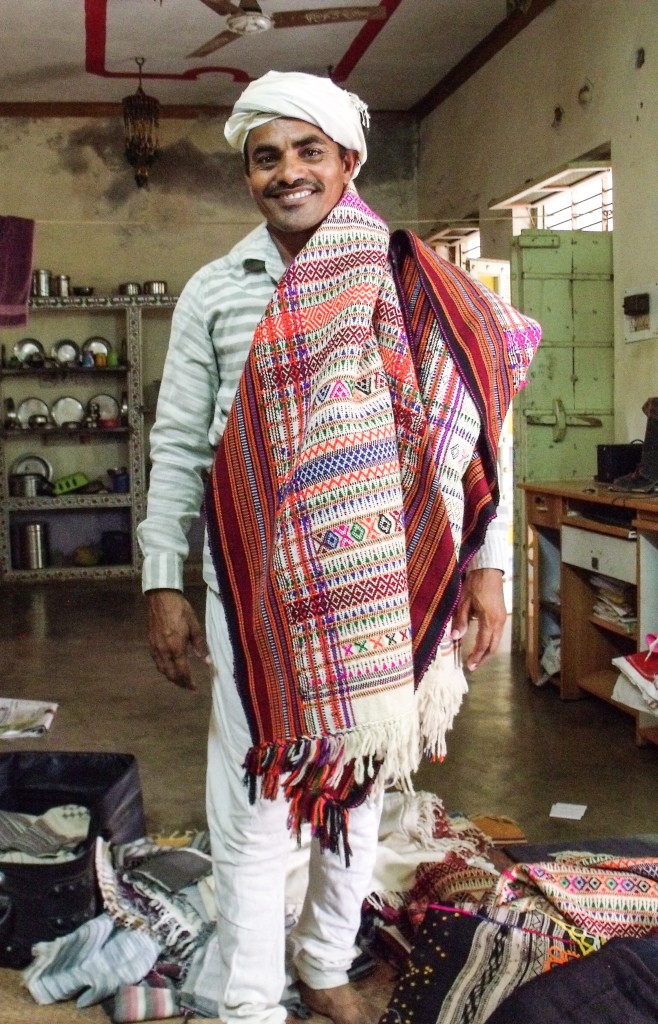
On my last morning in Kutch, I visited Bhujodi in hope of saying some quick goodbyes and thank yous to the weavers who had helped me during my visit before my bus to Rakjot in the early afternoon. This proved difficult as there is always so much to see and talk about, and more weavers to visit. I assured them and myself that I would be back next year, but I knew that once back home I would miss this amazingly industrious and buzzing little village, the warm and welcoming artisans and the beautiful weaving.
The next post will continue along my weaving journey of Gujarat to the highly skilled and endangered Patola – double ikat weaving.
4 Comments
Marilyn Murphy
Thank you for such an informative update on these projects. I had the honor or working with Dayalal at the Folk Art Market this past July. I am so impressed with his designs.
I’m pleased you enjoyed the post. You have some really informative posts on Cloth Roads too, and I love your products! Yes Dayalal’s work is so innovative and exciting. He’s come so far since studying at KRV, its great!
Pingback:
beeingcom
great blog.. really usefull… collection of handloom Shawls
http://www.gleamberry.com/index.php/accessories/shawls.html