When I visited Shamji in Bhujodi (see previous post) and told him of my research, he gave me the names and contact details of a few weavers I should visit in Saurashtra, the region to the south of Kutch in Gujarat – an area I had not yet visited. The first was Laljibhai Parmar who lives in Rajkot and is a member of an extended family of Ikat weavers. Laljibhai is not actually a weaver, although he hails from a weaving family, but his extended family are practicing weaving. Laljibhai makes the phanni – the reed section of the beater that beats the weaving in between each passing of the shuttle.

Lalji cuts the reed into 500 small pieces which are different spaces apart depending on the required thickness of cloth. The reed is attached by string to two long pieces of bamboo which are different lengths depending on the width of the cloth to be woven. Each thread in the warp is passed through each gap between the reed.
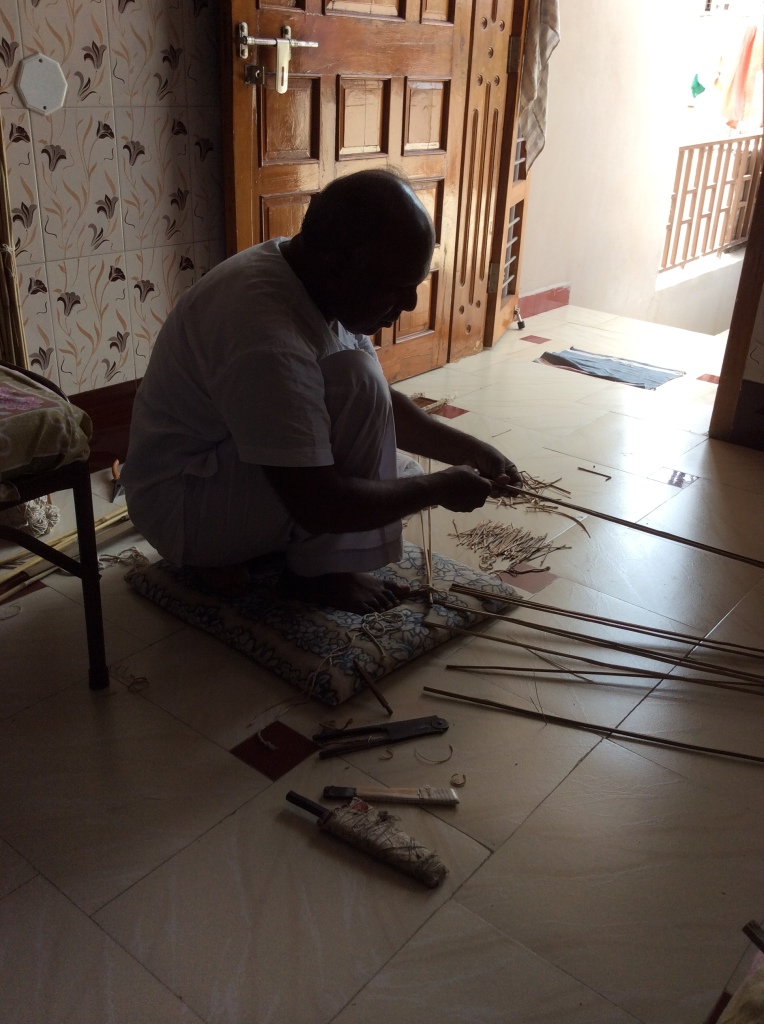
Some looms use a metal phanni, including the looms used by the patola weavers, but all looms in Bhujodi use the reed ones made by Laljibhai.
Patola Ikat Weaving
The street where Laljibhai, his wife Virabhai and son Jayesh live are not used to receiving foreign visitors. As I arrived I found that gradually more and more neighbours were appearing from their houses to take a peek at me. As Laljibhai and Virbabhai took me to see their weaving neighbours, I was spoilt with tea and spent a large part of the visit posing for photos.

Rajkot, along with nearby Sundrenagar, is known mainly for single ikat silk (and synthetic mock silk) weaving, a cheaper and less laborious version of the patola weaving which is double ikat, where both the warp and weft yarns are tied to resist the dye. The patola double ikat in its traditional form originates from Patan, a small town north of Ahmedabad in Gujarat. It is traditionally dyed with natural dyes – again another aspect that distinguishes the craft from Rajkot and Sundrenagar.

While I didn’t visit Patan this time, I was there in 2008, and visited members of the only extended family of weavers left in the town – the Salvi family. The patola cloth is thought to date back to the first century BC, and was a highly prized commodity in the South East Asia trade for over five hundred years. In Indonesia the cloth was used for ceremonial use and court dress and believed to possess protective powers. Locally, the silk patola sari would be given as a gift to the bride at her ceremony. They were also used as ceremonial saris by Nagar Brahmins, Hindu or Jain Mahajan (merchants) and Bohra Muslims in Gujarat and Maharastra.
In a leaflet I still have from my visit to the Salvi family on Patan Patola, they include a folk song which conveys the attraction of patolu saris:
Chhelaji Re, Mare Hatu patanthi patola mongha lavjo
O my dear! Do bring the precious patola from Patan for me!
In Rajkot the weavers producing for Sindhoi Patola Arts – founded by Bhalabhai Parmar in 1991, produce both single and double Ikat. Laljibhai’s nephew Tarun doesn’t weave but takes an active part in marketing, promoting and selling. He was the only English speaker so accompanied us while visiting different members of his family at their workshops, all producing for Sindhoi Patola Arts.

Process
The design is meticulously drafted out onto graph paper for the weaver to refer to as he or she goes along. For double ikat, the warp and weft silk threads are tied separately with cotton thread in the portions marked out by the design. These sections that are tied will resist the dye. Then the next portion which is to be the colour of the first dye is tied so that it can resist the next colour, and so on, in a similar way to bandhani, but on the yarn instead of the cloth. Once the dyeing is complete, and the yarns untied, you can already see the design spread across the yarns, before it is woven into cloth. The weft yarns are tied onto bobbins and the warp yarns go through the warping process and onto the loom. In between sections of weaving the weaver uses a pin to re-arrange the threads to achieve the distinctive feathered edge that patola is known for.
Sindhoi Patola Arts has also taken inspiration from other weaving traditions, such as the Maharastra paithani sari weaving which uses the supplementary zari patterning. The zari was traditionally real gold thread, but now is a cheaper imitation. It still however gives a luxurious sheen and makes it popular for wedding saris.

The market for patola weaving is high end. A double ikat sari can take months to make, so inevitably is very expensive, and thus the reason single ikat is now more common. Sindhoi Patola Arts are now also producing dupattas to broaden their market. Their designs consist of both those traditional to Patan Patola weaving, and new designs they have developed based on customers’ preferences. Saris are generally only produced on a commission basis, because of the length of time they take.
Traditional designs include the panchanda – an all over geometric square grid design that is used in multiple variations, often combined with floral, bird and elephant motifs.
While there are various cheaper imitations of patola available, including printed versions, the original hand woven patola still prove popular amongst an elite market in India. It still holds the desirability it has for many centuries, and provides a connection to an important part of India’s textile heritage.
I didn’t want to leave the welcoming and accommodating community of Rajkot, who in only a day had made me feel as if I’d known them years. I said I would definitely be back, and perhaps before then they will have had many more visitors, like the weavers in Bhujodi, and I won’t be as much of a novelty.
If you liked this post, you might like these related posts from Travels in Textiles: