While in Rajkot, I called the other contact that Shamji had given me – Chandrakant Patel, who I was told managed an organisation that produce Khadi – a handspun and handwoven fabric, in Gondal, just 40 km from Rajkot. I asked if it was ok for me to come and visit for my research. About an hour later I received a call from Durgesh Jadeja, who informed me he worked as the fashion designer and PR at Udyog Bharti – the name of the organisation. He said he lived in Rajkot and was travelling to Gondal the following morning by car and would I like a lift. He also said I could stay at the guest house at Udyog Bharti as there were a few rooms. I said I’d love to – it would make a change from the characterless commercial hotel I had booked last minute in Rajkot! So the next couple of days were mapped out for me, and I met Durgesh the next morning outside my hotel in his white fiat.
On the way to Gondal, we past continuous factories and farms – Rajkot and it’s surroundings have had a lot of industrial development in recent years and it is now one of the most commercial districts of Gujarat. Durgesh gave me the story of Udyog Bharti. It was founded in 1957 by Hargovindbhai Patel, a dedicated Gandhian, following the swadeshi movement lead by Gandhi. This movement was part of Gandhi’s campaigns to shed political domination and return to a self-sufficient India, and home-grown, hand-spun and hand-woven cloth played a big part in this movement. The image of Gandhi spinning yarn at his charkha (spinning wheel) has become synonymous with this movement.
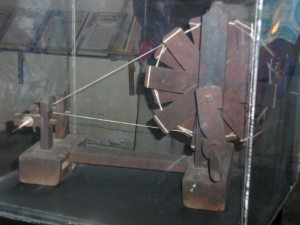
Udyog Bharti is subsidised by the Government under its Khadi and Village Industries Act, a Commission passed in 1956. This means that the government have strict control over khadi, and most khadi products are only available in government stores all over India. The products are similar across the stores.
When we arrived, Durgesh introduced me to Chandrakantbhai, the current director of the organisation and Hargovindbhai’s son. After we sat in his office with a customary cup of chai, and I explained my research interests, I was shown round the whole factory by Durgesh. The building was arranged in a square with a courtyard in the middle which provided a quiet and green space full of palm trees, plants, flowers and beautifully singing birds – a welcome escape from the bustling bazaar just a few steps outside.
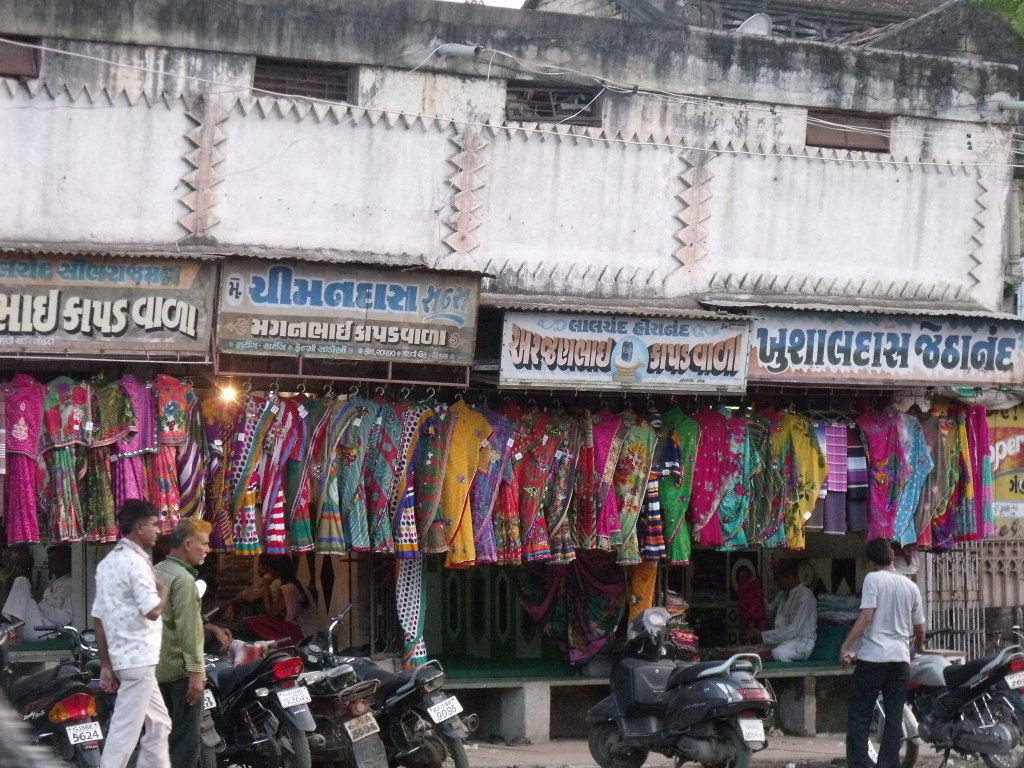
The factory houses the spinning, pattern cutting, tailoring, technical workshop, showroom and shop, store rooms, adminstration, stock keeping and accounting.
Durgesh first took me to the spinning workshop where there are several manual multi-spindle machines. It is all women of varying ages who work on these machines. Udyog Bharti is a secure employer for them and also provides each employee with a bank account and issue interest-free loans. The machines can spin 10-12 reels of cleaned and carded cotton. The cotton is twisted as it passes through ridged rollers. The girls are paid 150 – 200 RS per day.
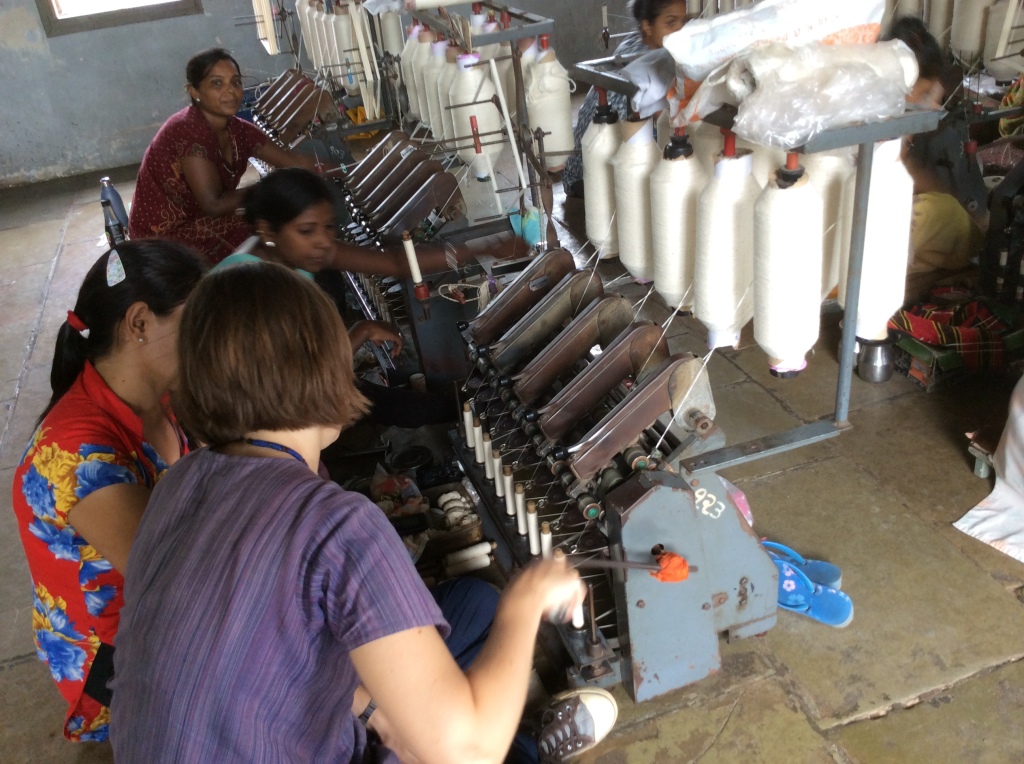
I sat and had a go at the machines while chatting to the ladies and Durgesh translated. It is quite physical work and I wondered if the girls get tired. They said they didn’t, and it seemed like they had established a comfortable rhythm in this repetitive task. It is rare now to see hand-spinning done on the traditional charkha, but at least women are provided with employment this way. There is a risk that eventually mill yarn will completely replace hand spun. In an article in the November/December 2013 issue of Selvedge about the French company Khadi and Co, founder Bess Nielson expresses worry about the khadi industry, that young girls are no longer interested in the industry. I think that if Udyog Bharti can expand their design repertoire for a contemporary urban market – often government initiatives in India have little innovation in design – then they will continue to do well and expand their ethos over the world, as well as providing sustainable employment for the spinners and weavers, and all other supporting staff.
In the technical workshop, we met Dipesh, the technical manager who has 24 years of experience working here, and has developed all his knowledge practically though this work, without education. His team are able to provide all the technical specifications of each cloth they weave and fibre they spin. The equipment includes a magnifying machine which allows you to see how many counts of thread there are per square inch and a machine that stretches the yarn to test it’s strength.
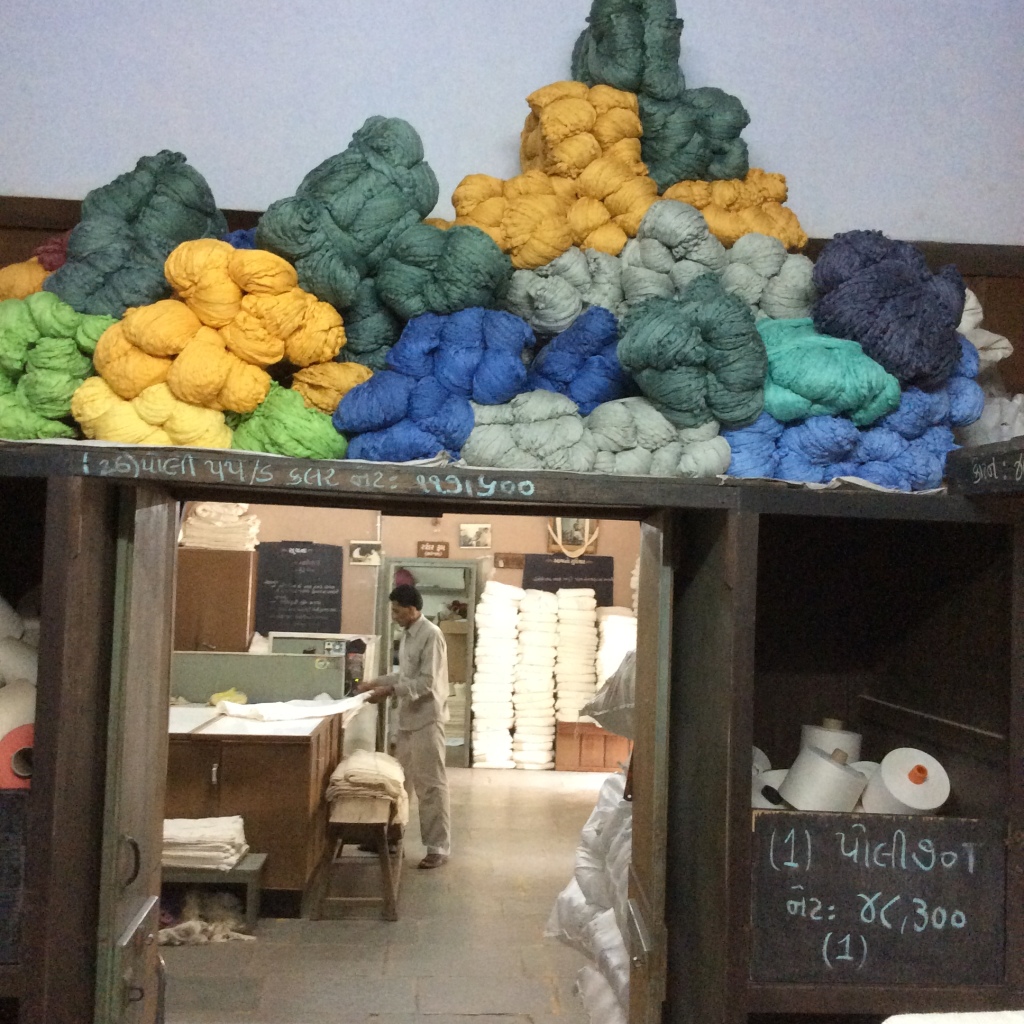
Khadi fabrics produced and sold here range from checked, striped, slub textured and ikat fabrics where the yarn has been dyed first, for men’s shirts and women’s kurtas. They also commission craftspeople in Kutch to piece dye the cloth and block print. Embroidery is done by women in Jamnagar and nearby villages. Screen printing is done in nearby Jetpur – a traditional printing town. They also get khadi silk from Bangalore.
The complex at Gondal included the ‘khadi plaza’, a shop and showroom, where all the khadi products are sold, such as garments for men and women, bed sheets, curtains, towels, rugs and bags, as well as cosmetics and other products bought in from elsewhere that adhere to the khadi philosophy (they even sold a solar powered stove!).
I was then taken to see one of the organisation’s weaving workshops, not far away in Gonal. It is all women working on foot treadle looms. These looms are operated by the feet moving peddles which, via a pulley and lever system, simultaneously move the shafts and the shuttle along the width of the cloth so freeing up the hands.
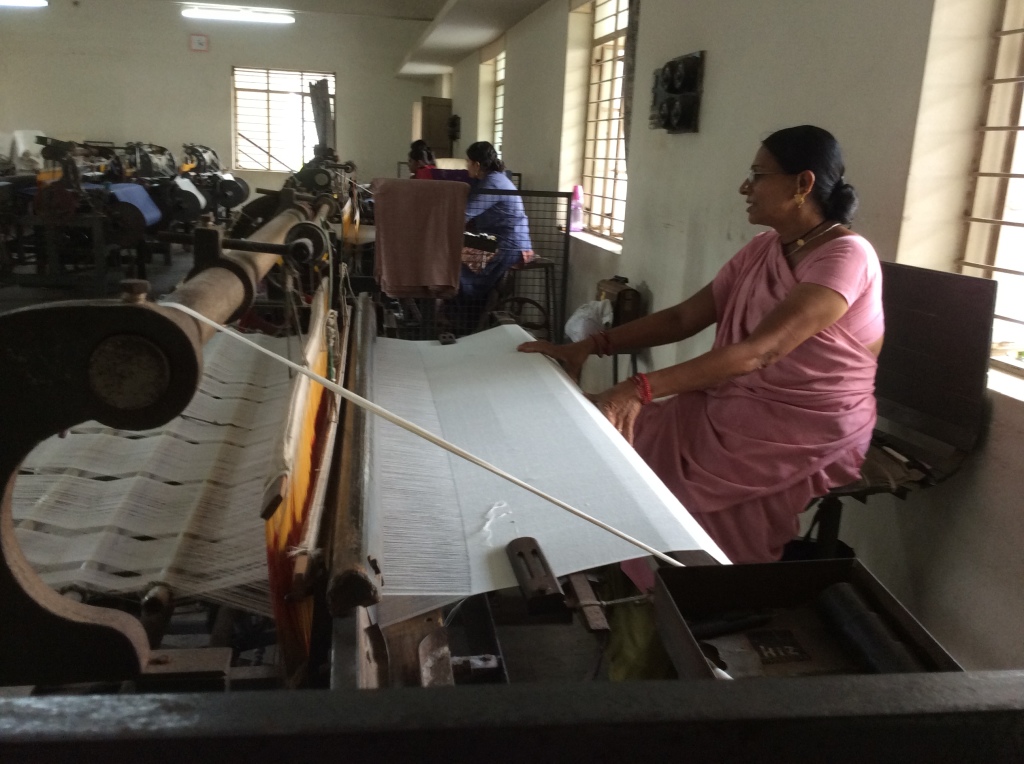
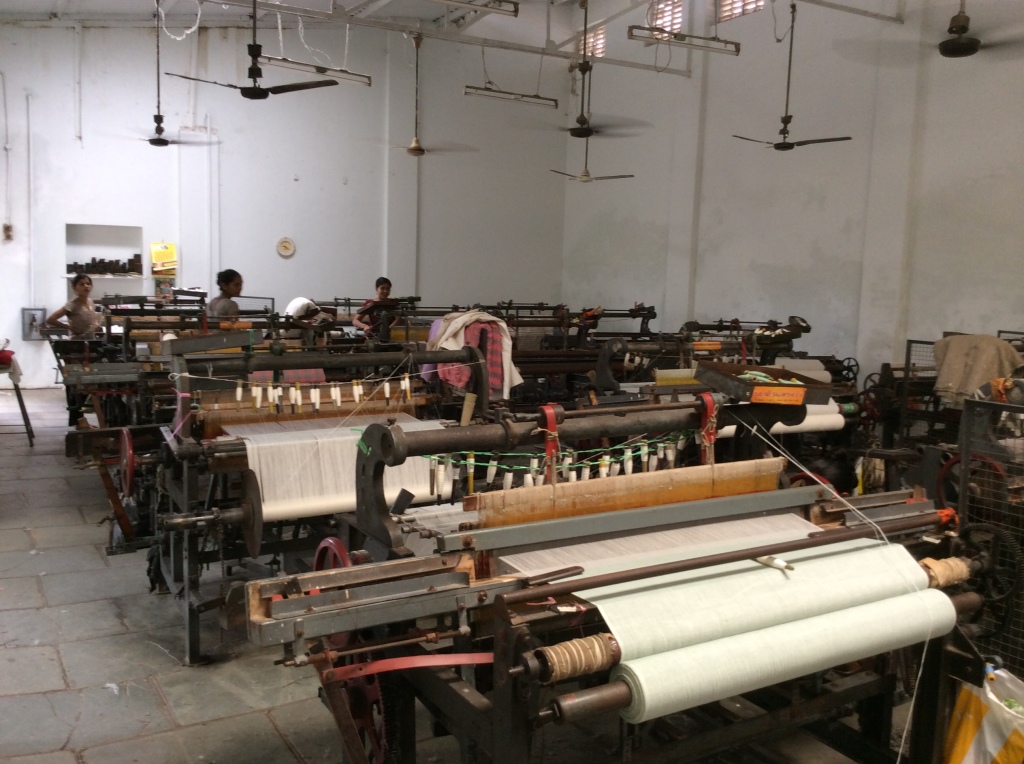
It was great to see almost the whole process of the organisations’ textile making process, we even saw workshops that made the spinning machines and looms for Udyog Bharti, their sister organisation Bel Kelavani Mandir (that I will come to shortly) and weavers and spinners all over India.
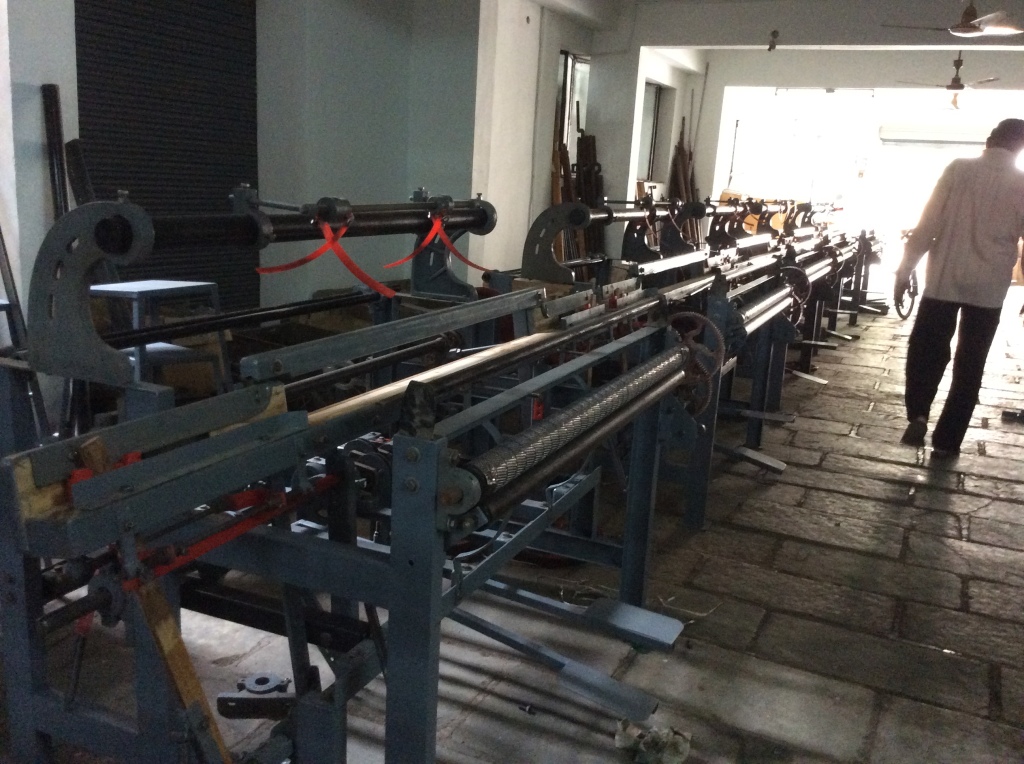
Udyog Bharti had another khadi plaza strategically located a few miles out of the town and along the main highway to the tourist hotspot Junagadh. This housed a showroom and shop and more workshops.
The next day we were up early to travel to the small town of Bagasara, 62 km south of Gondal. Here and the surrounding villages are where many of the weavers working for Udyog Bharti live and work. We first visted Bal Kelavani Mandir (Temple for Child Development). The centre is laid out in a very similar way to Udyog Bharti in Gondal, and like Udyog Bharti was founded upon Gandhian principles by Shri Lalchandbhai Vora in 1931. It houses a spinning workshop and a school, and runs educational activities for children and adults. The education is aimed at the nomadic tribes surrounding Bagasara, usually marginalised by the government.
After a simple thali, and many photos posing with large groups of school girls who were all either excited, amused, bemused or sceptical at the first white person they’d seen; we headed to see the weavers a little way out of Bagasara.
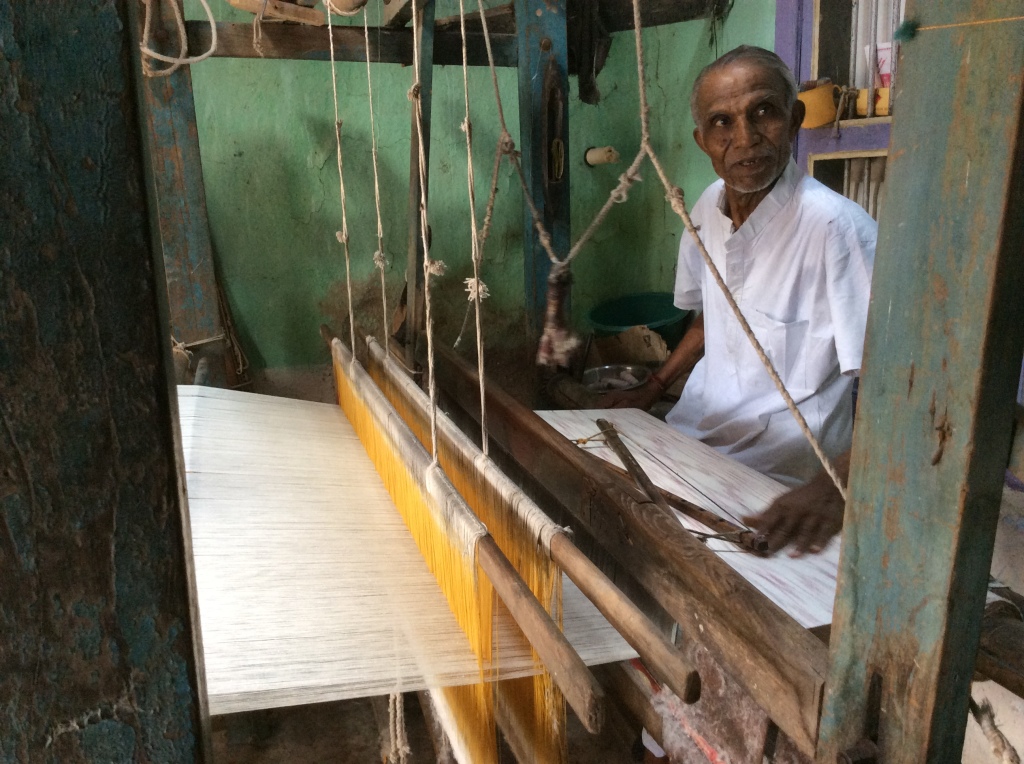
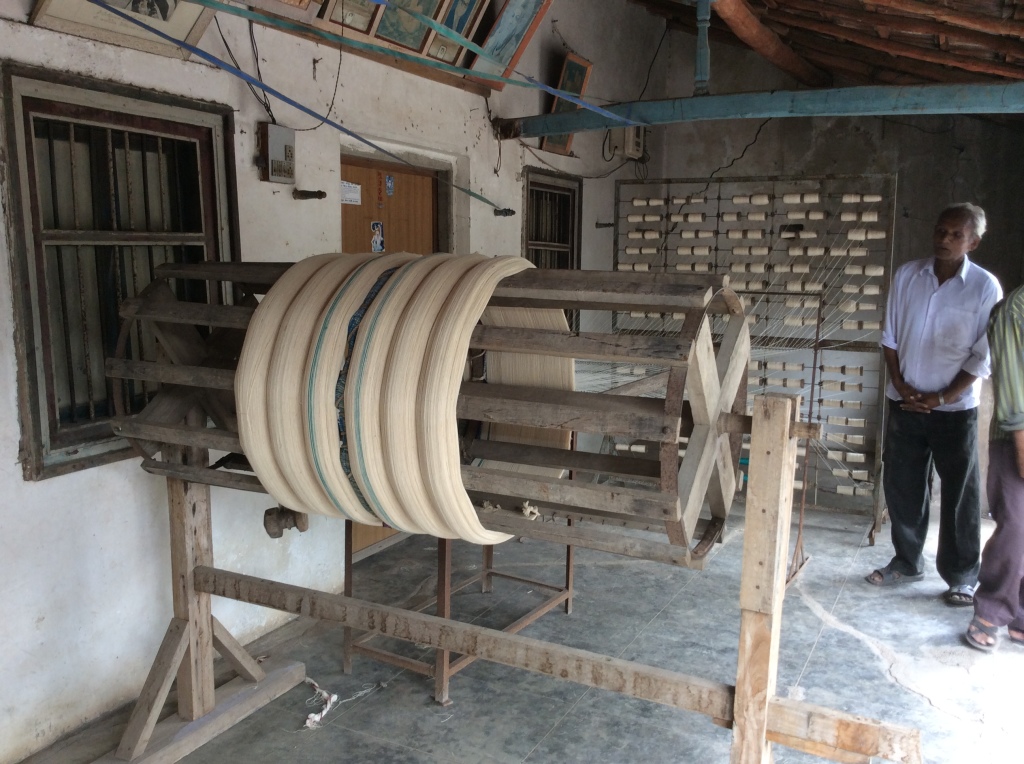
The weavers here work on looms more similar to those used by the hand weavers in Bhujodi – wooden frame and pit looms. The fabrics woven here were denim and ikat for dress fabrics, and towels. The village was alive with activity, and like all artisan families I’d visited in Gujarat so far, I received kind warm welcomes by the weavers and their families, and they showed an eagerness to show and talk about their work.
By the time we had visited all the weavers, had over indulged on chai – not being able to refuse the many kind offers of sweet creamy tea offered to us at every home we visited, I was ready to return to Gondal, exhausted. However, we had one more visit to make. This was to a screen printing workshop in the same village. Most printing is done in Jetpur a town not far away with a long history of block printing. Jetpur is a major production centre and exporter of the kanga cloths for East Africa. Jetpur’s printing has now greatly reduced, leaving many traditional printing artisans without work or finding alternative employment. This was partly due to the excessive pollution caused by the dyes as the use of chemical dyes increased and the government banning their use, as well as being overtaken by faster mechanised printing methods.
Udyog Bharti get some printing done in Jetpur, and some at this small unit in Bagasara. I was amazed at how fast the process was, and how much water is needed. We watched as two workers washed and bleached the fabric in preparation for printing.
The brothers who run the family printing business told us their struggles to keep the business going. They are often losing customers to larger printing units, using mechanised screen printing processes. This is a situation often encountered in small textile producing units all over India, and a subject that will no doubt continue to crop up on Travels in Textiles’ posts.
Already feeling exhausted after a long day, I couldn’t begin to imagine how tired the workers in this printing unit were. And the man in the above photo has been doing this job (mainly washing) for 15 years! We finally set off on the long drive back to Gondal where I packed my bags (ever-growing full of textiles I pick up along the journey), ready for a drive to Ahmedabad the following morning. I would miss the people I had visited in Gondal and Bagasara, as well as those I’d visited all over Gujarat, their welcoming and accommodating nature and their amazing work ethic and dedication to their craft. Having gotten so used to Gujarat, I was apprehensive, but excited about my next destination – Maheshwar in Madhya Pradesh…
Read other articles in this series: