In Ashok Nagar district in northern Madhya Pradesh state, nestled in hills, surrounded by forests and lakes and scattered with historic monuments, is the charming town of Chanderi. It is one of two towns in the state famous for its weaving heritage – the other is Maheshwar, which you can read about here.
I took the awkward journey from Maheshwar where I was staying long term for my research, which involved a bus to Indore, a delayed train from Indore to Ashoknagar and from there a local bus along badly maintained roads (or damaged by recent rains), to Chanderi. At one point we passed a bus that had tipped off the edge of the road. Luckily it hadn’t completely fallen over, and the whole of its passengers piled onto our bus resulting in a not very comfortable remainder of the journey. The town’s inaccessibility is possibly one reason it doesn’t receive the many visitors you would except for such a picturesque town steeped in dramatic history. Although travelling from Delhi is much easier – you can get a train directly to Lalitpur in Uttar Pradesh which is 40 km from Chanderi.
I stayed at the government-run aptly named guest house Tana Bana (Hindi for warp weft), the only tourist accommodation option in the town – another possible reason for the limited number of tourists. Reviews on Trip Advisor of bad maintenance and management are accurate. It had a sort of Fawlty Towers ish feel, and the manager even looked a bit like Basil Fawlty. I was shown three rooms, and the one that seemed the most habitable still had a gaping hole in the wall, which backed onto lots of greenery. This was disconcerting considering the reviews had also mentioned insect infestations. Luckily I only met the odd cockroach.

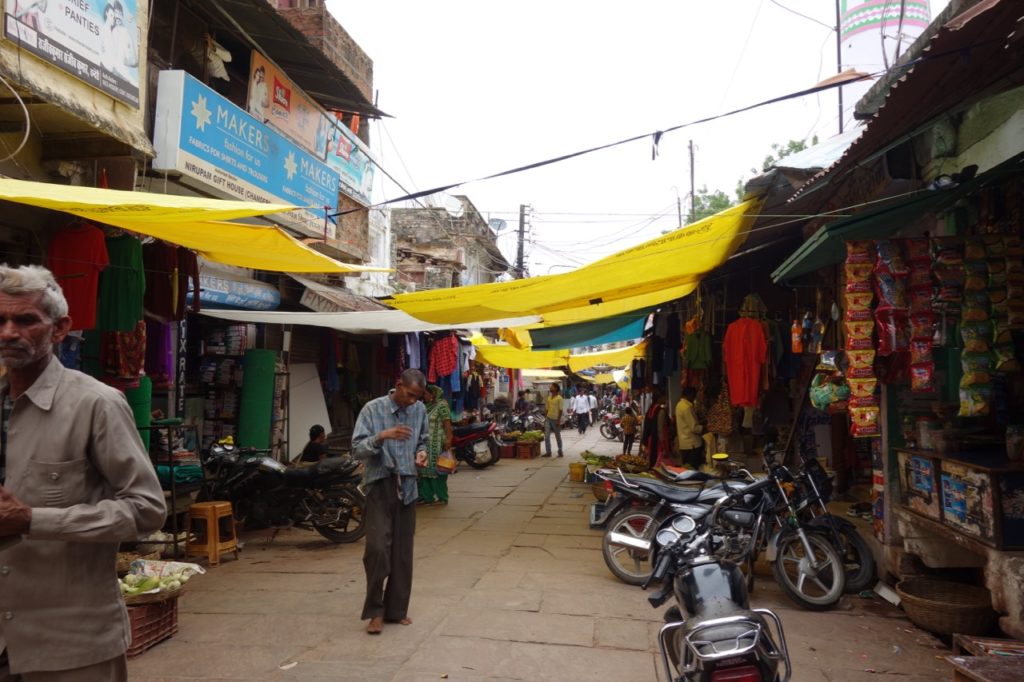
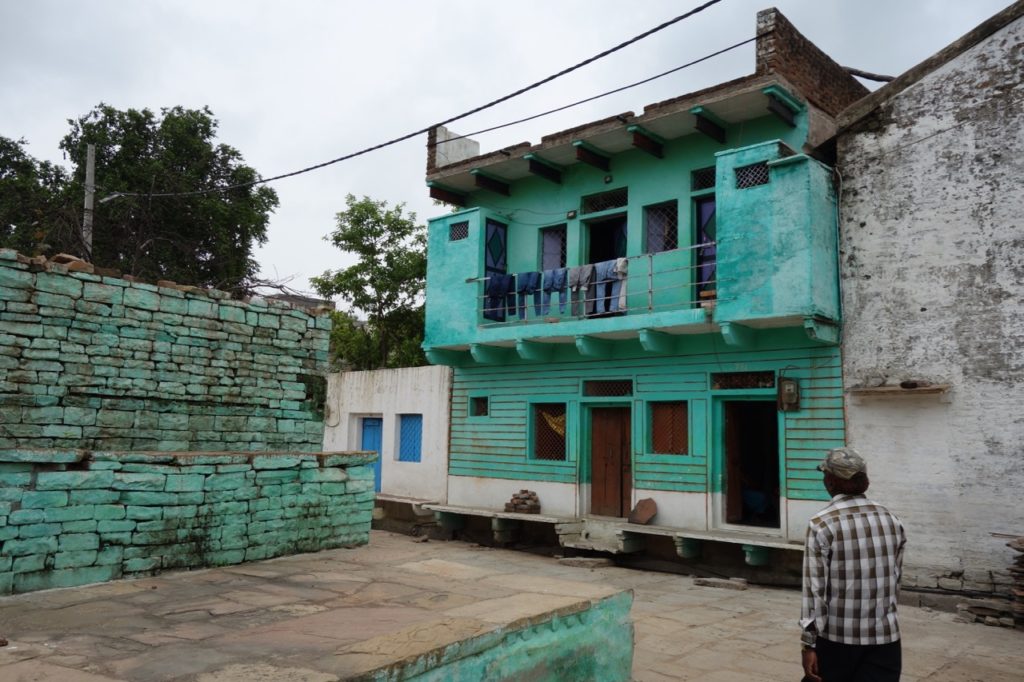

The Town
The town of Chanderi is located on the borders of Malwa and Bundelkhand. Its history goes back to the 11th century when it linked the important ancient trade ports of Gujarat to Malwa, Mewar, Central India and the Deccan. It became an important military outpost. The town is also mentioned in the Mahabharata when Shishupal was the king.
One tragic event that stands out in the town’s history is when the Mughal Emperor Babur captured the city from Medini Rai. The gap in the hill where his army entered is visible from the hill-top fort. Babur’s invasion led to many women and children inhabitants of the town take part in the Rajput rite of jauhar which involved escaping dishonour in the hands of the enemy by jumping in a fire pit to commit suicide.
The history of the town has been well documented and researched by the man who kindly hosted me during my visit, Muzzaffar Ansari, known more widely as Kalleybhai. Kalleybhai is a government registered guide, and while he has had little schooling, speaks 6 languages, has done extensive research on Chanderi and its history, has published several books, is a traditional weaver and an advisor at Chanderiyaan, a Non-Governmental Organisation supporting weavers. He has worked with Michael Willis, a curator in the South Asia department at the British Museum. His book Chanderi: History, Heritage and Culture as well as his guidance throughout the two days of my stay have informed this article. I met Kalleybhai at the Rani and Raja Mahal, the location of Chanderiyaan, along with Himadri, a designer from NIFT (National Institute of Fashion Technology), Bhopal who was doing his internship there. There are also two government centres providing assistance to weavers, one is run by the central government – Development Commisioner (Handlooms), and the other is state run – HSVN which was inaugurated by the prince of Gwallior in 1911.

The Raja Rani Mahal (one of 43 palaces remaining today out of an estimated 260 palaces originally), was restored in 2009 at the time Chanderiyaan was forming. The looms sit on the upper of several floors in one of the many conjoining haveli-like structures that make up the palace. On the ground floor is the stitching and pattern cutting room, and the showroom. In other rooms in the palace’s dizzying maze, are a design studio, a photo studio and office where the marketing and website are done, and communal spaces for eating and relaxing. The staff would congregate at points, and often they call to each other from one courtyard to the next, which the walls provide good acoustics for.
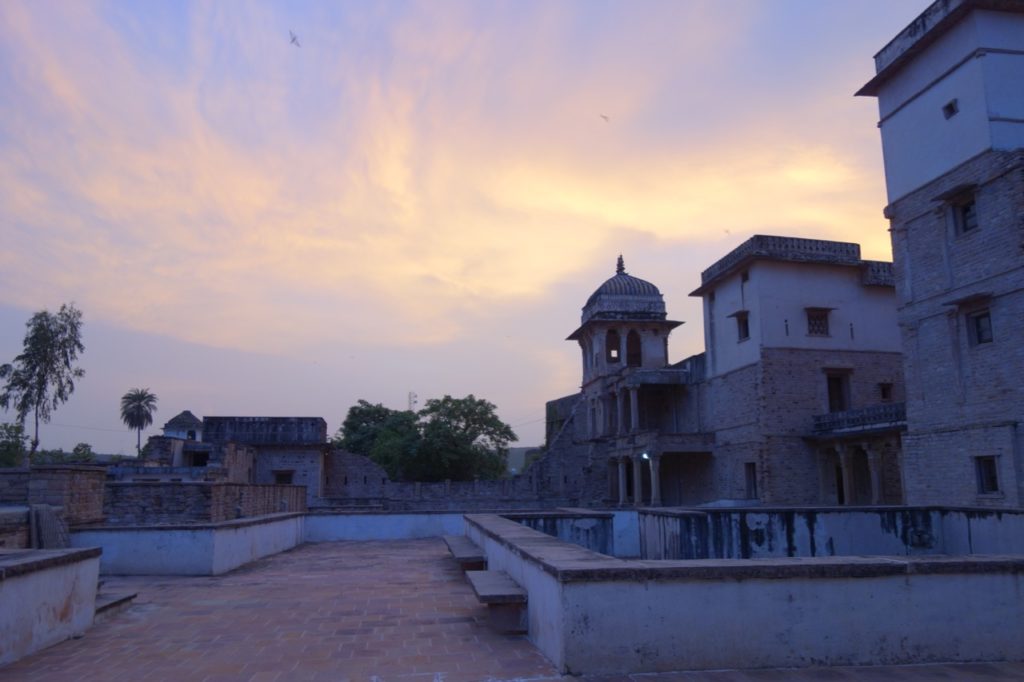
Chanderiyaan was set up in conjunction with the Digital Empowerment Foundation which work to train weavers in using computer technology to assist the design process. The technology is used to create the graph designs, and convert them to the jacquard punch cards. Jacquard is used for the borders, pallu and bootis.

Origins of Chanderi weaving and its materials and process
There is little known about the origin of weaving in the town. Kalleybhai says there are speculations that weavers were brought here by a Bengali King in the 14th century. Much of the weaving done before the 19th century was similar to Bengali muslin, woven only in white, and praised for its fineness. The courts of the Princely states of Gwalior and Baroda were the major buyers of the fabric, which was used for safas, pagdis (both types of male headwear), dupattas, lugadas and saris. Over the 20th century more colours were used. In his book Kalibhai says Ram Narain Mishra, a prosperous sari trader, claimed to have introduced coloured yarn to the production of Chanderi fabric. Initially the coloured threads were used only in the weft while the warp continued to be white resulting in a pastel coloured fabric. Gradually colours were used in both the warp and weft. While in the past natural dyes were used, today all dyes used are chemical. Like Maheshwari weaving, the yarns used today are raw silk which is 20-22 denier thick in the warp, with a count that can vary from 4000 to 17000, and mercerized cotton or raw silk in the weft. Sometimes zari is used in both the warp and weft to make a ‘full tissue’ sari. In the borders and bootis, mercerized cotton, silk and zari (metallic) threads are used.

Designs in Chanderi weaving involve a lot of floral, geometric and intricate motifs. They can also be bold and striking. While the yarns used are similar to those in Maheshwar, the designs and look are what distinguish the two.
Today, like most handloom clusters in India, the fly-shuttle has completely replaced the hand-throw shuttle. So far, I have only seen the hand-throw still in use in Kota. In Chanderi hand throwing the shuttle would enable different colours in each border and the body, and two weavers would work together at the same loom.
The following day, the three of us visited Naya Puri, the Koli colony. The Koli community are Hindus, and they and the Muslim Julaha community dominate the weaving industry here. Both men and women work in weaving as well as other ancillary tasks. The first sign of the industry we saw was a woman engaged in rach (heddle) making. The rach is the part the warp threads pass through and is attached to the peddles. It is made up of nylon threads attached to two wooden poles. A painstaking looking process, it takes 5 days to complete one rach and the maker will receive about rs 750 for it. Luckily this task does not have to be done too often, as one rach will last for a few hundred saris.

We then visited the family of Balkrishan and his wife Sumitrabhai who run their own business and have four looms. Most looms in Chanderi are pit looms. Balkrishan is a traditional weaver and taught his wife weaving after they got married. He has also taught many others in the town. They have three sons and a daughter. One of their sons, Arvind who helps with the business, showed me some of the saris and dupattas as well as the original graph designs that had been done by Furkaan, the designer at Chanderiyaan.

We then visited the only warping mill in the colony managed by Ram Ratan, situated in a very traditional building with a log roof. These houses make up 60% of the houses in Chanderi, the rest are concrete. This architecture is one characteristic of the town that helps it maintain its heritage.
Development efforts
Talking of architecture and heritage, another government scheme in the town is the building of a huge ‘Handloom Park’ situated just a kilometre or so outside the town. We went to visit the construction site and were told the park would be open in September 2016 (it was July at the time). The plan was to house 250 looms, which weavers in the town could rent at a subsidised rate, a trade facilitation centre, an area for a display gallery and accommodation for visiting buyers. These would all be housed in huge typically government style concrete buildings, the exterior walls of which had been covered in ‘heritage style’ tiles in keeping with the architecture of Chanderi. I wasn’t convinced this huge structure wouldn’t create a scar on the surrounding quiet, lush green landscape on the outskirts of the town. I was also not sure whether this is another government scheme developed centrally by people with little knowledge of handloom and the specifics of Chanderi’s handloom industry, as has so often happened in other government handloom schemes which have failed in the past. Indeed this was the sentiment of some residents I spoke to. A few saw it as a positive scheme, while some said it wouldn’t make much difference to the industry – weavers would just weave at the centre instead of at home. Although as Kallibhai pointed out, ‘weaving and home life are interconnected,’ the loom is literally rooted in the domestic structure. Further, the attraction to continue weaving for many is the fact you can work from home in a relaxed environment and surrounded by family and the community members, most of whom are involved in various tasks in weaving. Marketing is something the government schemes have usually been less effective in, but is something the weavers need most help with according to many weavers I spoke to as they attempt to reach the high-end markets that will appreciate the value of handloom. Whether this Handloom Park will be successful in marketing is yet to be seen, but will be interesting to see what happens.

I met three young weavers who had attended The Handloom School in Maheshwar. Two of these are brothers Raghuveer and Keshav Koli. Because they graduated only recently, they haven’t had much chance to incorporate the techniques learnt during the course. But combining working for others and for themselves, is helping to build up capital to further develop their own business. One of their clients is luxury sari brand, Raw Mango.

Mehmud Ansari, a graduate of the second THS batch is a member of the local cooperative society who he said don’t pay a good wage if the products don’t sell well. Thus good marketing is key, and something he learnt while at THS. He also learnt the importance of detecting faults in weaving and to maintain a high quality standard, as well as practicing interacting with buyers in Delhi. One thing all these weavers had complained of was how short the course was, at 1.5 months, something the directors have taken on and so the course now lasts 6 months. The full impact of the school on these weavers, is yet to be seen, as they struggle to manage bringing in a steady income to provide for their family with branching out to using new techniques and materials, and adapting their technology to suit, and reaching new clients.
While many weavers here still face challenges including; competition with powerloom imitations being passed off as handloom, and reliance on middlemen paying meagre returns with little other option in an isolated town; their weaves are celebrated amongst handloom experts and enthusiasts, and with help from schemes such as Chanderiyaan, Digital Empowerment Foundation and The Handloom School, they have carved out a distinct identity and high profile as skilled and innovative weavers.
8 Comments
Keryn
Your posts are incredibly detailed and full of fascinating information. I really look forward to each one. I love India and her textiles. Mind blowing!
Thank you. Great to hear from a fellow Indian textiles lover, and so nice to know you enjoy reading!
Priyanka
I absolutely love going through your posts. I’ve read quite alot of them and impressed with the insight they provide. Are you still in India? I would be grateful to catch up and hear all of the amazing stories you have to share in person.
All the very best and looking forward to future posts.
Thank you Priyanka. Good to hear from you, and glad you enjoy reading the posts. I’m not in India right now. I can let you know when I’ll be going again though (nothing confirmed as yet). You can email me on: ruth@travelsintextiles.com
Shila Desai
I have one complaint, Ruth — your posts serve to elongate my bucket list! I’d love to visit all the weaving centres of your posts, perhaps even organise a tour for fellow textile aficionados. Keep up the good work!
Haha, thanks Shila! I hope you do get to visit these weaving centres at some point. I’d be happy to help out if you do take tours to any of them too.
Jayshri
I was totally engrossed reading this write up.though we roughly know this to be the sitiation of handloom everywhere,this article summed up all.aspects so well.thanks for sharing your experiences.
Thank you Jayshri!