I recently visited Kota on my way from Jaipur to Maheshwar keen to learn about the Kota Doria sari weaving tradition.
I was kindly helped by Victoria Singh, a local resident and founder of the Kota Heritage Society. After accompanying her on a few errands around town – she is involved in a lot of local charity and heritage work, she took me to the village of Kaithoon which is about fifteen kilometres from Kota, and the main centre for weaving in the region.
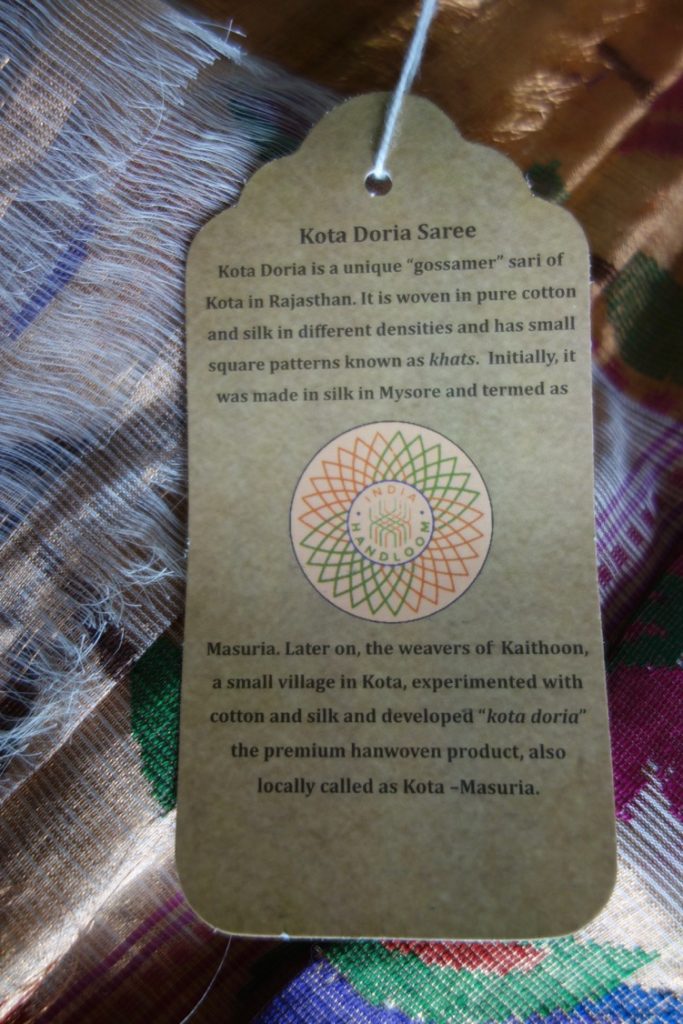
Victoria Singh and Ritu Jain write more on the kora doria in an article for Hand-Eye magazine.
We first went to meet Badrun Nisha, the secretary of the Women’s cooperative Kota Women’s Weavers Organisation (KWWO). The women members used to work for master weavers or middlemen, but are now doing most of the yarn sourcing and marketing themselves. Badrun also has her own small business and sells directly to high-end designers. Bibi Russell is one designer who Badrun has worked with, and who has strongly promoted the kota doria fabric.
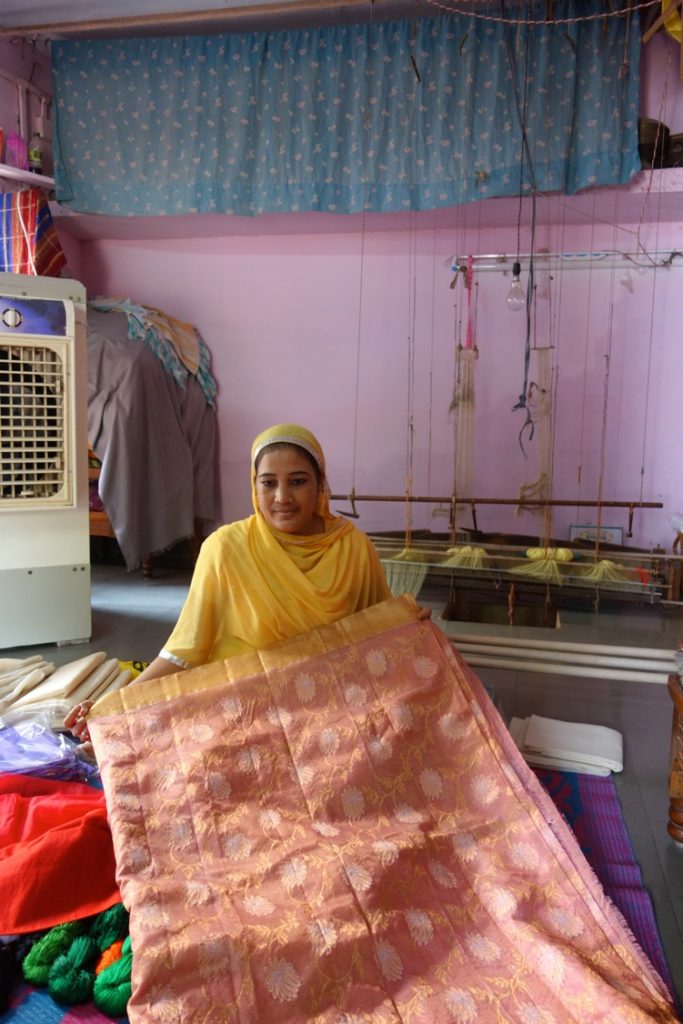

There are two things that distinguish Kaithun from any other weaving centre I’ve been to (except for the actual cloth), the loom – they are still using the hand-throw shuttle, while most centres in India began adopting the fly-shuttle from the early to mid 20th century. The loom without the large frame that holds the fly shuttle, takes up very little space, and can be packed away quite easily. Secondly, the majority of the 1500 weavers (mostly from the Muslim Ansari community) in Kaithun are women. Badrun Nisha as well as many other women work part time and fit weaving around their domestic chores. Women value the work of weaving – they don’t need to leave home to do the work. Further if there is extra income coming from their husband’s work – Badrun’s husband is a tailor, this removes some of the pressure and weaving can be done around other household tasks. However, what Vicky strongly stressed, is that its purely a job for these women – they consider themselves weavers, that’s what they do. There’s no sense of boredom, but they take little interest in creating their own designs, and will happily weave something a designer gives to them.
Badrun showed us a sari she had woven for the national award, but it didn’t get chosen. The award was given to a master weaver. The sari took her three months and has an all-over floral lilly pattern and gold zari. There has to be real gold in zari for it to be considered a true kota doria, one of the criteria of the GI (Geographical Indication) mark, which the fabric was given in 1999. Interestingly, these were commonly in use in Kaithun compared to other weaving regions where I’ve not seen it regularly in use. The kota doria, like many other handloom fabrics is often imitated by powerlooms, and passed off as handloom. Further, sometimes a power loom kota doria is hand-printed and then labelled a ‘handloom’ product. Indeed kota doria is a popular fabric for block printers in Kutch as I found on my visits, but I was told by weavers in Kaithun that it is unlikely this will have been handwoven. But if handwoven kota doria is printed – the focus is less on the weave than on the print – so the printers will get the recognition. Thus, there must be a large market for powerloom kota fabric for prints. But the labelling needs to be accurate – which is where the use of the handloom mark – see picture above, and the GI becomes useful (although there are now so many marks – it starts to get confusing!). Even Azgarbhai – the next weaver we went to visit, buys plain power loom saris and gets them block printed, to bulk up his stock and meet the demand.
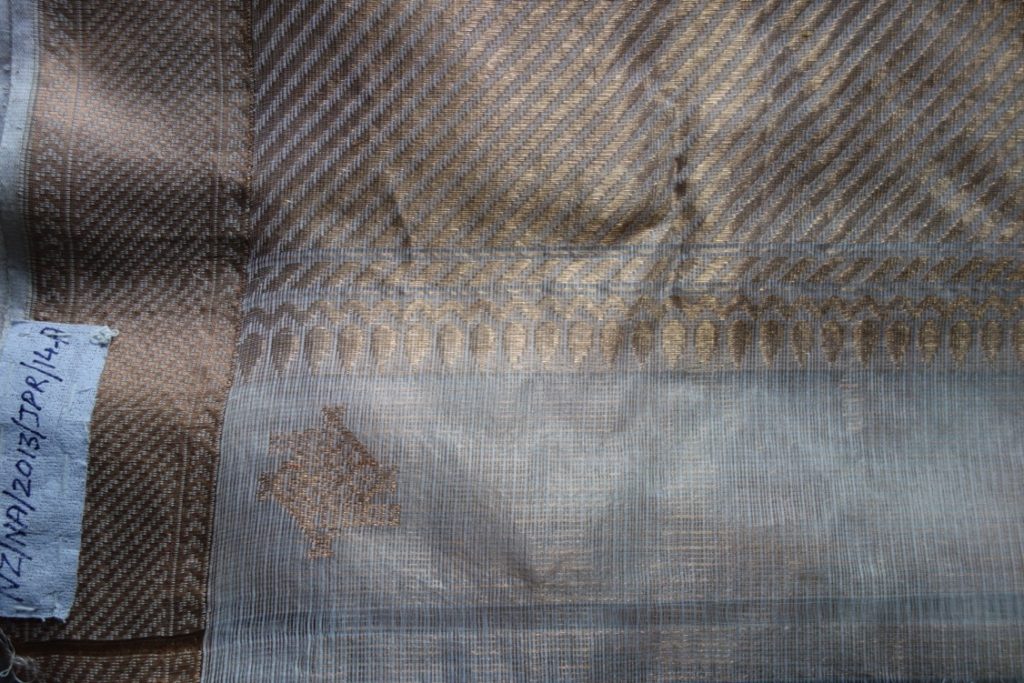

We were also shown some simpler, plainer saris and dupattas. These had simple checks in the weave – khat which is the traditional characteristic of the kota doria. Small butis are also often woven in the body, using extra weft. Dobby is used and sometimes jacquard for the more intricate patterns. Zari (metallic thread), is commonly used in borders and pallu. The heavily patterned saris are something new and popular among the Marwari community, or in South India where the coolness of the cotton is preferable. We saw one of these heavily patterned saris in the workshop of Azgarbhai, a master weaver and national award winner whose large family of five brothers and their sons are all involved in the weaving business.
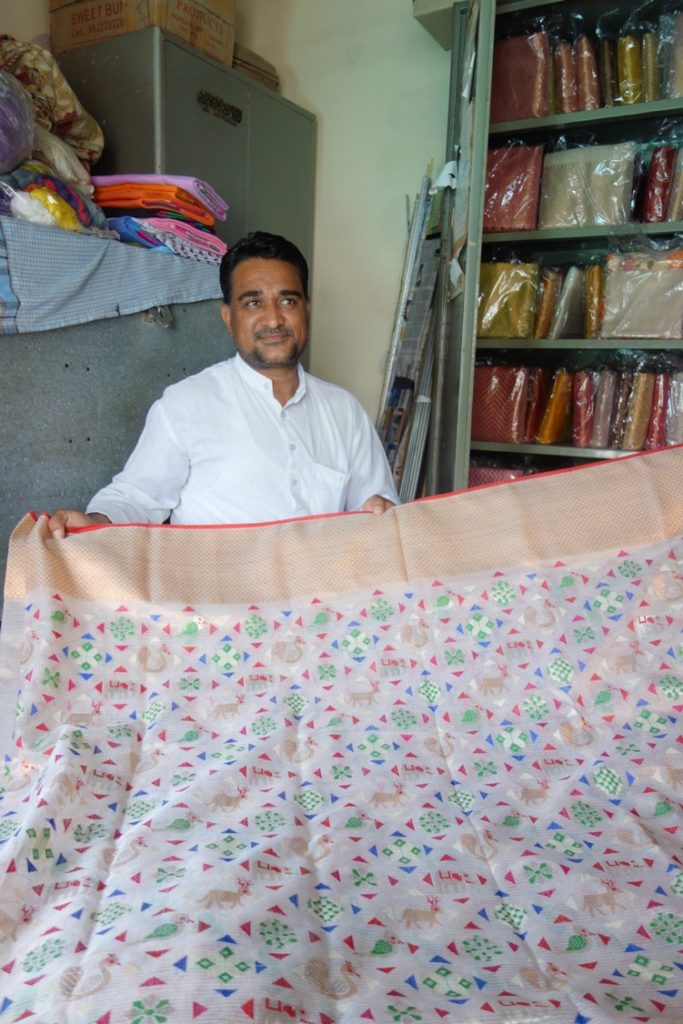
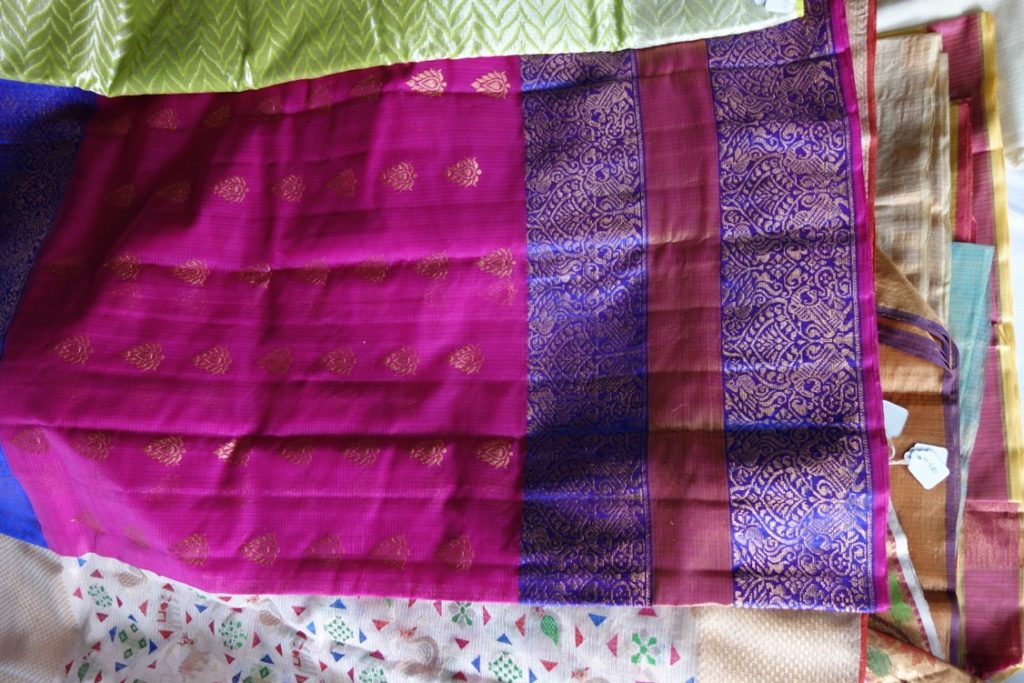
Azgarbhai’s son joined a workshop at The Handloom School in Maheshwar about three years ago. It included design, business and technical training (read previous posts about Maheshwar and Women Weave/The Handloom School here). Azgarbhai has 150 weavers working for him, 90% of whom are women. Azgarbhai showed us a range of intricately patterned, expensive kota doria demonstrating his large production capacity, diverse market, and highly-skilled weavers working for him.

In comparison with other weaving clusters in India, Kaithun has little promotion and documentation. The main problem Kaithun weavers face is the competition with powerloom. I wondered whether introducing the fly-shuttle would help this, as well as catching up with the volume of production and thus promotion of other handloom clusters, but then it would change the unique nature of kota doria, and possibly affect the achievement of the fineness of the fabrics. Further, would increase in promotion be beneficial or would it provide breeding ground for more powerloom cheaper imitations? These are just a few of the many complex but important questions to explore in the search for the most effective ways of developing handloom as a sustainable craft and livelihood in India.
As mentioned above, little has been written on kota doria, but see the following links for further information:
www.handeye.com/content/kota-doria
www.kotaheritagesociety.in/khs/kota-doria/articles/kota-doria
http://ipindiaservices.gov.in/GI_DOC/12/12%20-%20Form%20GI-1%20-%2022-07-2004.pdf – Kota Doria documentation written up for the application of the GI in the Ministry of Textiles’ GI journal
https://strandofsilk.com/journey-map/kota-doria/introduction
2 Comments
Rachel singh
Love your blog
Sunila
Interesting and very informative article.